
From design to manufacture
Our team can help with:
- Design for manufacture
- Manufacturing process development
- Test and inspection process development
- Prototype and pilot production
- Supplier selection
- Transfer to production
- Process validation and risk management
- Process and quality control documentation
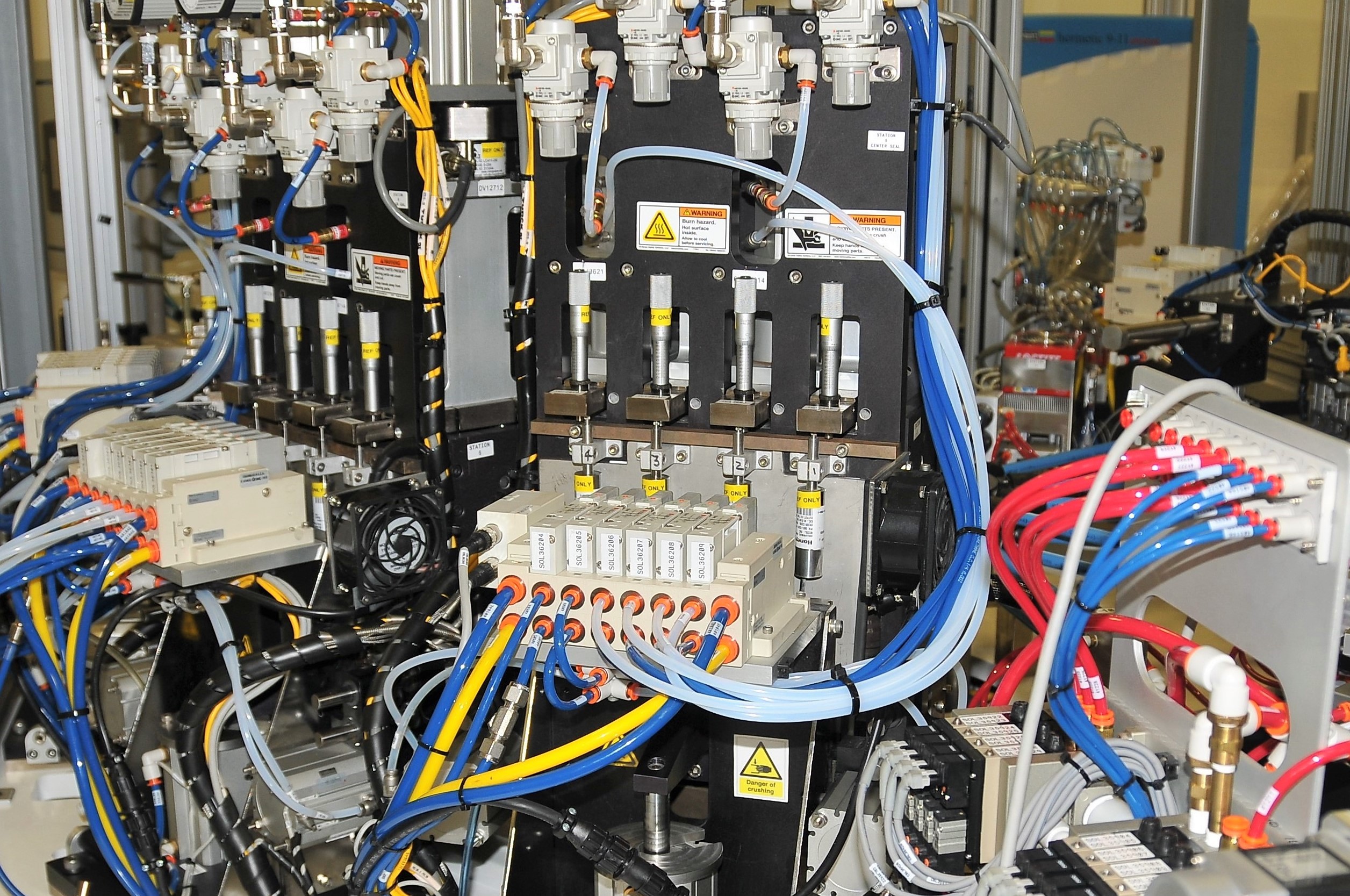
Design for production
Moving a design into production crosses boundaries between teams, and often, between companies. Navigating these boundaries is tricky. Without careful planning it can result in a loss of know-how and a fruitless blame game when things go wrong.
Springboard work across both sides of the transfer to provide continuity and clear accountability. We support your development by planning for design for manufacture and assembly activities early.
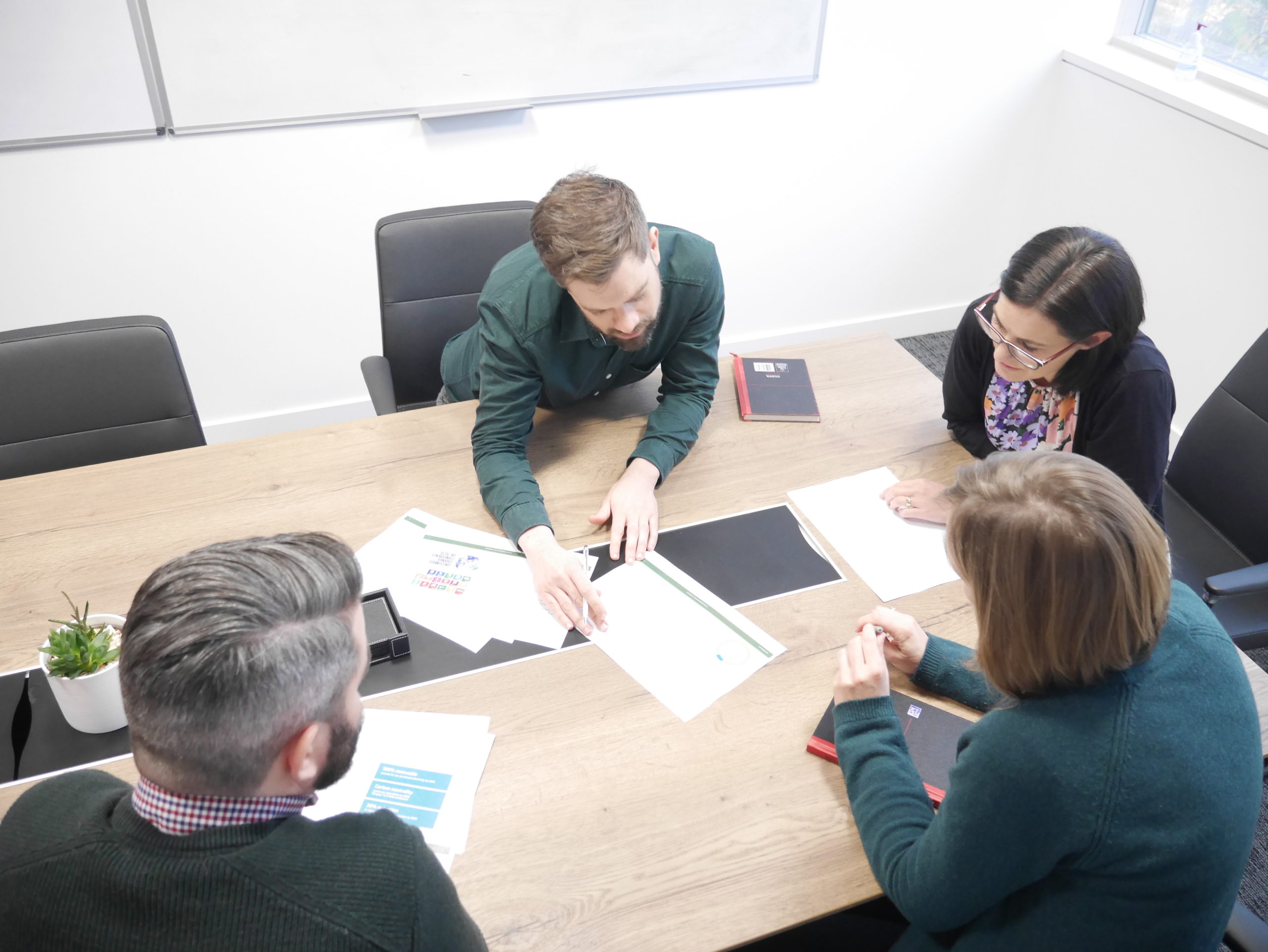
Part production and prototyping
When it comes time to produce parts, we design and run bespoke processes and development rigs in-house that best match the needs of product. We also build inspection and test equipment to check and monitor the parameters critical to quality. Prototype production is covered by our ISO 13485 certification. Our strong grounding in science and engineering means we can rapidly diagnose and analyse areas for improvement.
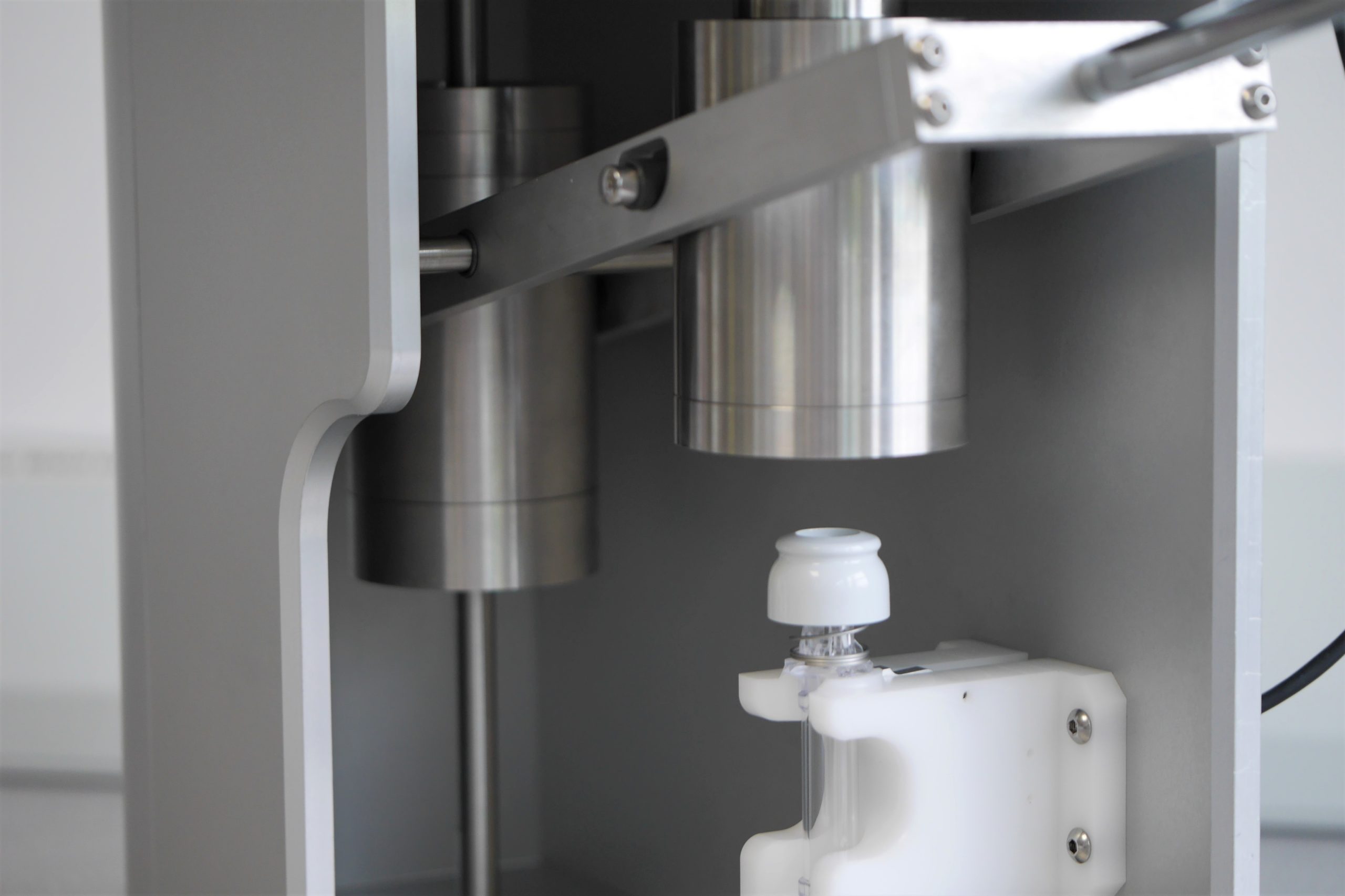
Partner for Commercialisation
Our parent company Sanner Group is a best-in-class agile CMO. Therefore, we can offer end-to-end in-house production with input from molding and automation experts right from the start. Multiple rapid prototyping methods, and access to aluminium tools to molding equipment offer various opportunities before scaling up into commercial manufacturing.
Beyond the partnership, we have worked with manufacturers around the world and can give you independent advice to bring products to life.
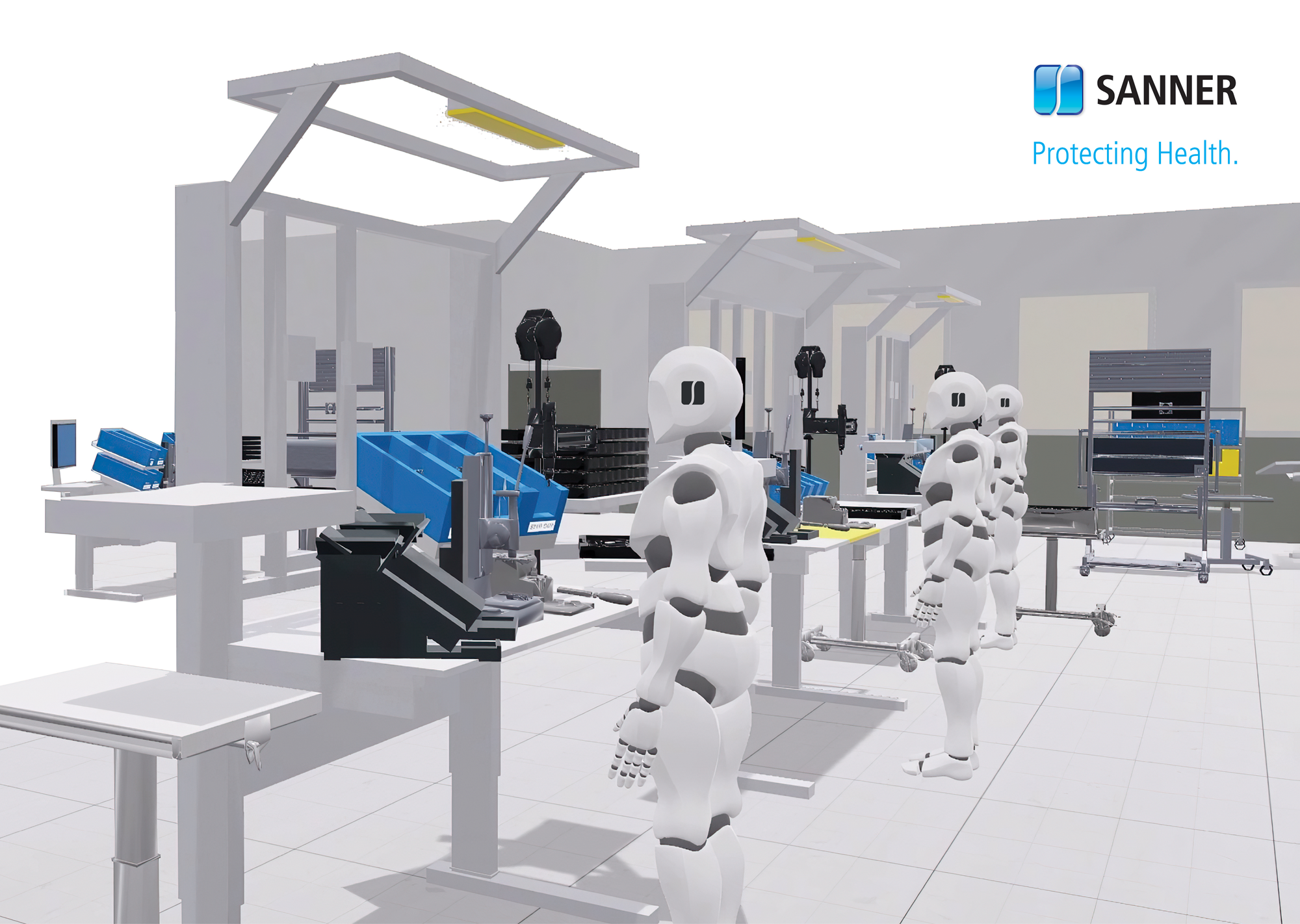
Comprehensive handovers
We maintain our involvement in a successful handover of production equipment by supporting IQ/OQ/PQ activities, operator training, trial runs, manufacturer sign-off trials, and on-going support for scale-up to production volumes.
Springboard creates process documentation, including:
- Standard Operating Procedures
- Equipment maintenance and troubleshooting manuals
- Process FMEAs
- Product and process quality control plans
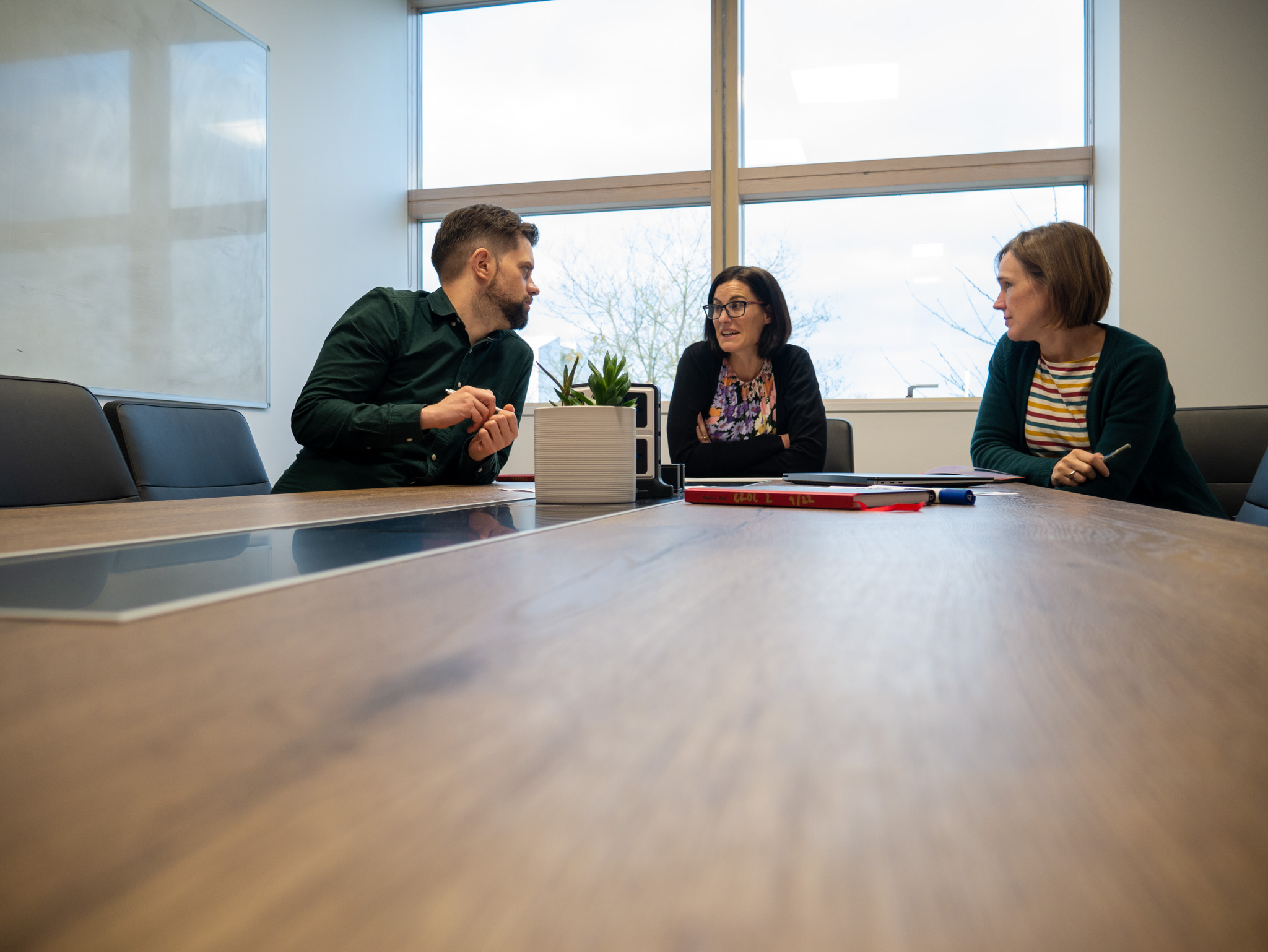
Global and local manufacturing
Sanner has recognized the urgent need for adaptable, scalable production. We have invested in new manufacturing facilities in North America, Europe, and China, that are capable of handling high-volume manufacturing for pharmaceutical and medical device customers. With demand at an all-time high, working with an experienced partner allows companies to mitigate the risks of production delays and quality lapses.
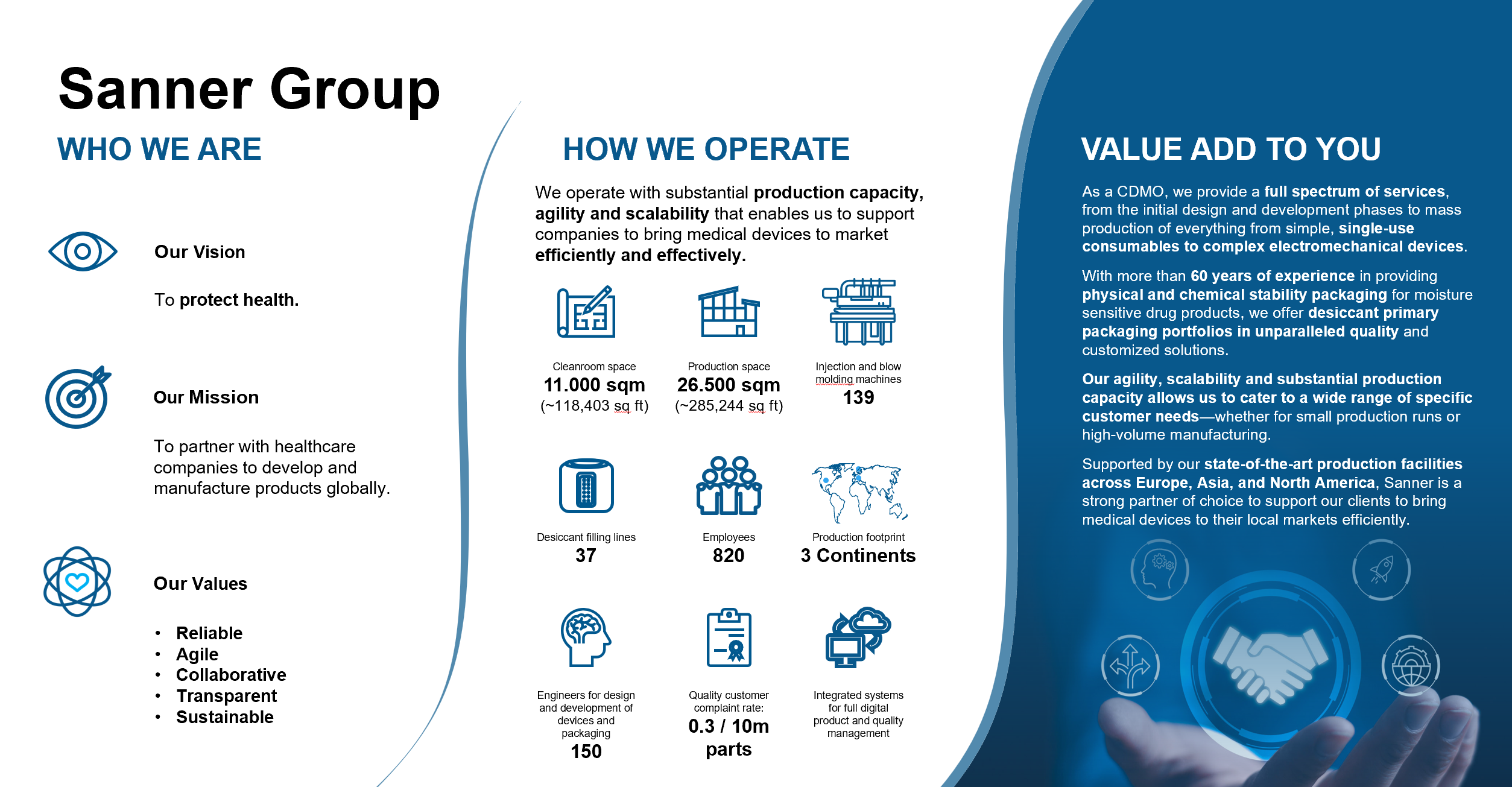