
Strategic and technical help with the autoinjector design
Client: A pharmaceutical company
Description: Our client was developing a new autoinjector to deliver their highly viscous drug. The high pressure and force required to deliver the drug in an acceptable time created unprecedented stresses and other demands on the device.
Activities: End-to-end device design, Science, Engineering, in-house testing
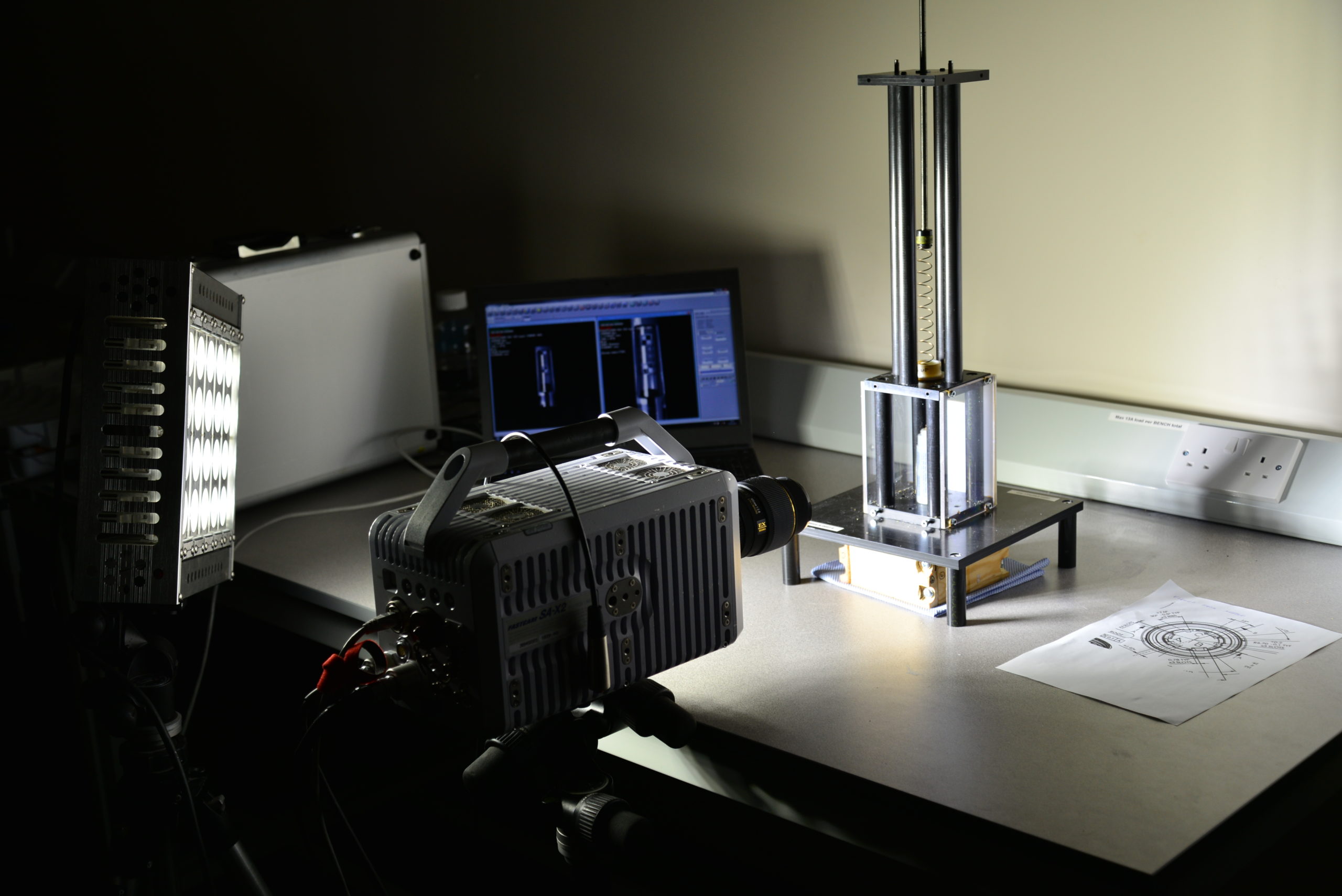
Innovative solutions to combat costs
The failure rate was very low, and each syringe of drug cost at least EUR 1,300, so a normal root cause investigation was unfeasible.
We had to create innovative ways to characterise the problems, and measure improvements, with very small sample sizes. This required a combination of practical device experience, advanced statistics, theoretical mechanics, and experimental physics. Even the cleverest test and post-processing lacks insight unless one understands the physics and expected results. Therefore, we created mathematical models and Monte Carlo simulations so we knew how the device should behave, and the experimental results were compared to those expectations.
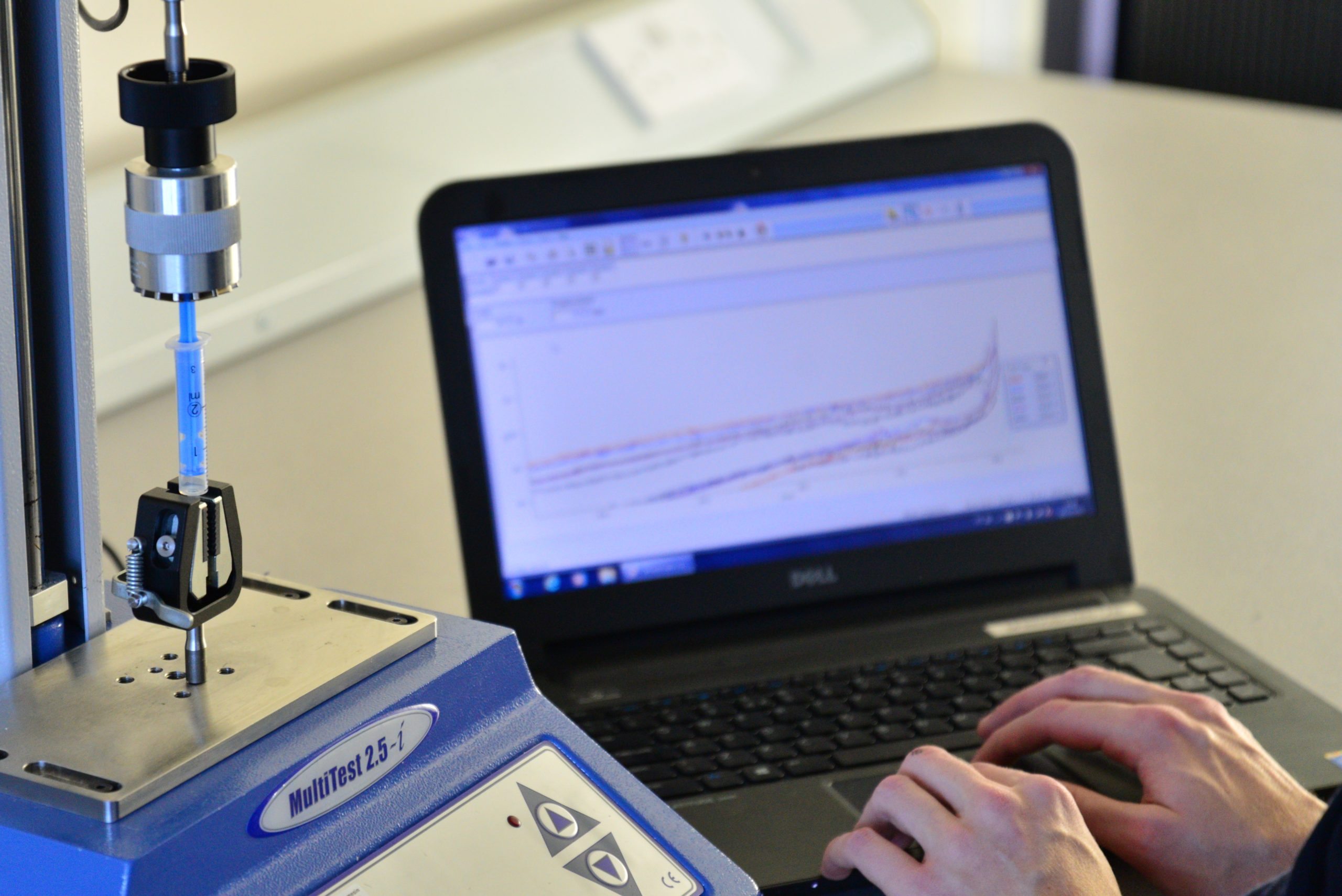
Results
In a relatively short time, we correctly identified the root causes of the problems. We then created various solutions and gave our pharma client a helpful map of which options would solve the problem, and which were fastest to implement. The main changes had minimal impact on the production tooling and did not affect the automated final assembly line, both of which had been validated.
Verification, validation, and reliability testing proved that the problems had been solved and the autoinjector was launched successfully in multiple markets, leading to hundreds of millions of Euros of additional sales.
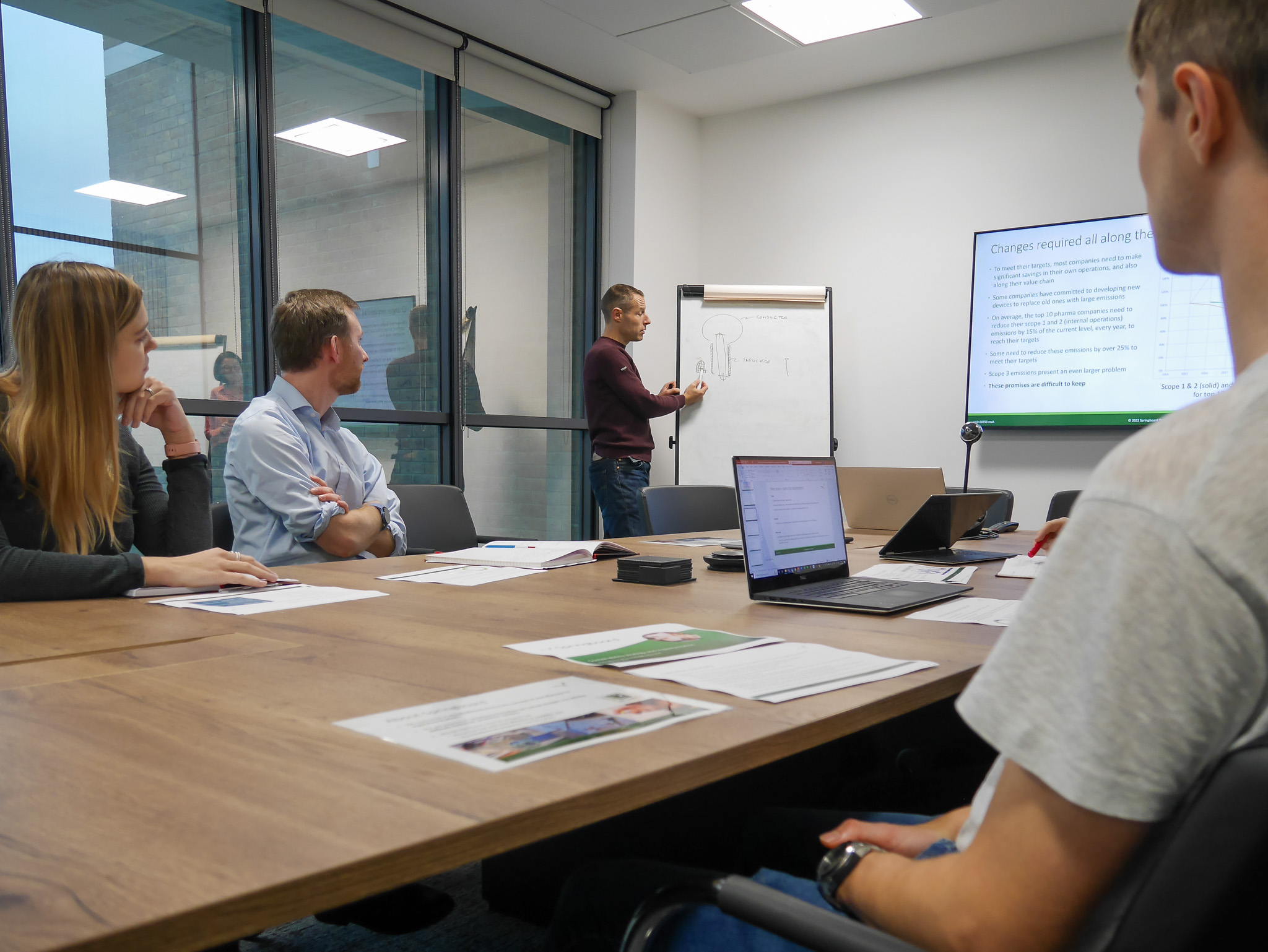